In our video interview, Mahoney details the new collision engineering pilot program designed to attract and train the next generation of collision repair technicians.
In January, Enterprise Holdings announced the launch of its Automotive Collision Engineering Pilot Program, a collaboration of the Enterprise Rent-A-Car Foundation and Ranken Technical College. The program is designed to attract and develop entry-level talent to fill essential roles within the collision repair industry, and enhance retention and advancement among collision repair technicians.
In our video interview, embedded below, Mary Mahoney, vice president of Enterprise’s Replacement & Leisure Division North American Operations, details the how the pilot differs from traditional technician training programs, why Enterprise got involved in the effort, and how it is evaluating the success of the pilot program. Mahoney also discusses the impact of the pandemic on Enterprise’s business and how the company adapted to the challenge.
Mahoney explained that the Automotive Collision Engineering Pilot Program differs from traditional training and apprenticeship programs by providing more frequent training and work rotations.
“We’re following the Ranken Technical [College] model. It’s a little bit different. It’s an apprenticeship program where there’s eight weeks in the classroom and eight weeks full-time working in a shop. So it’s eight weeks on, eight weeks off consistently in a rotation basis,” said Mahoney.
The program is currently being piloted at four schools across the country including Ranken Technical College in St. Louis, Mo., College of Lake County in Grayslake, Ill., Contra Costa College in San Pablo, Calif., and Texas State Technical College in Waco, Texas.
Mahoney explained that the pilot was structured based upon the feedback of its industry advisory board and its analysis of Rankin’s approach to the apprenticeship.
“I brought many folks from the industry, some that are on our advisory board our friends at CREF [Collision Repair Education Foundation], we all looked at this model and we thought, ‘You know what? This makes sense.’ This could help solve our problems.’ So, we decided to go ahead and pilot this,” said Mahoney
A key component of the program, according to Mahoney, is the approach taken by Ranken Technical College’s CEO, Stan Shoun, “He’s ex-military and he runs this program as tight as can be, but he has a mantra and it’s called the three-Ps. Its stands for price, perception, and preparation. And the idea behind this is that education and business and industry must work together to solve these problems.” “They want to take down any barrier prohibiting students from financially going to school, and jumping into a career like this. So there’s scholarships and there’s financial aid, but also when the student is working in the shop, those eight weeks on a rotation, they’re being paid and Enterprise… a part of that payment will be subsidized by Enterprise,” Mahoney continued.
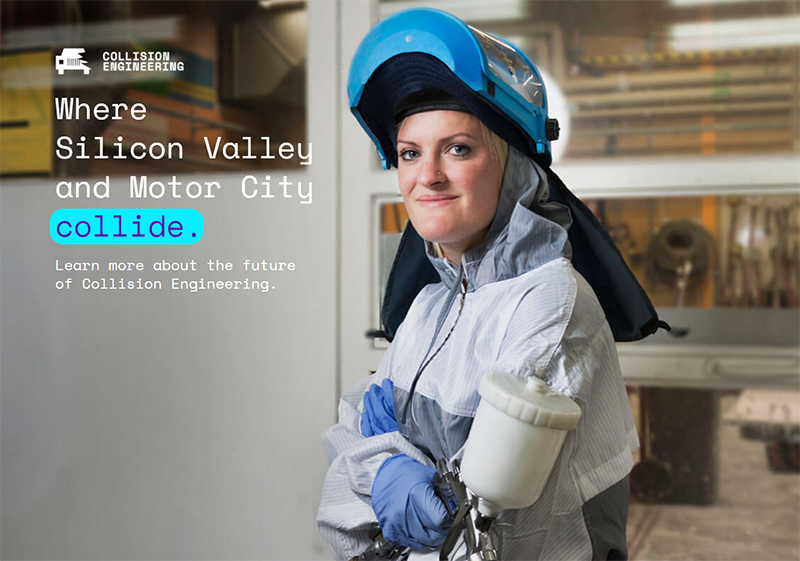
As part of the pilot program, Enterprise commissioned a digital marketing program designed to attract people to careers in the collision industry. Part of that effort includes the beacollisionengineer.com website pictured above.
“The second part, and I think it is probably the most important part, is perception. We have got to change the perception in order to move forward,” said Mahoney. “What Stan does in this model is, he starts at the middle school level and he works with people who are the influencers, the student councils, and the teachers and the students themselves from middle level school, all the way up through high school.”
As part of the effort to raise awareness of opportunities in collision engineering, Enterprise is funding a unique digital advertising campaign to create awareness and help recruit people into the program. The campaign uses slogans like, “Where Silicon Valley & Motor City Collide,” to update the perception of a career in the collision industry.
“The third [P], most importantly, is preparation. By the time these students get through their school, they graduate, they are ready to hit the ground running, work for an employer, and really be a worthwhile employee, fully educated and experienced,” said Mahoney.
Mahoney explained that Enterprise decided to get involved and support the effort due to the challenges all segments of the industry face recruiting and training staff.
“Collision repairers are facing an unprecedented challenge right now in trying to hire and build a workforce, a skilled workforce, in order to sustain their business long-term. And this is a problem that’s not going away anytime soon, and we’re all in this together,” said Mahoney. “We are a transportation rental car company, and unfortunately, our cars are not immune from accidents. So we repair thousands of cars each year.”
“As an industry leader, we felt the right thing to do was to spearhead this pilot and invest in the future to support our partners, to support the industry as we move forward. And again, I think the key is, we can’t do this alone. No single organization can do this alone. We all have to do this together, business industry, along with education,” said Mahoney.
According to Mahoney, the pilot will last two years with a goal to expand the effort globally.
“We have an enormous amount of metrics and KPIs from start to finish. And the goal is to get students into school, graduate, follow them into an employment and beyond. And if we can prove that out successfully, and we believe we will, then the goal long-term is to develop a program like this in every market that we operate in, in the U.S. and into Canada, as well as Europe, because this is a global problem,” said Mahoney.
Mahoney urges businesses that would like to participate in the pilot program to contact John Helterbrand, National Automotive Collision Engineering Program Director and Automotive Collision Repair Department Chair at Ranken Technical College via email.
Prospective students can sign up to receive information about the program at the beacollisionengineer.com website that supports the career marketing program.
Mahoney also discussed how Enterprise has adapted its operations in the wake of the pandemic supporting its business partners while working to assure the safety of the public and its workforce.
Mahoney explained that, like so many businesses, it implemented changes last year that would normally have taken months or years in a matter of days and weeks.
“We immediately worked on a new program called curbside delivery, just like a restaurant, for vehicles. We started to work with our partners in the industry, MSOs, and we gave them concessionaire agreements to minimize the number of people that are exposed at the time when a customer is putting a car in the shop,” explained Mahoney.
“We spent a lot of time building our clean car package, or clean car pledge,” said Mahoney. “We worked with Clorox on that and we continue to move forward.”
Looking toward the future, Mahoney says that business levels are starting to improve and they continue to work with collision repairers and insurance companies to serve their needs today, but also look toward the future.
“We stay close to our partners, the collision repair folks, our insurance company partners, and we follow their lead in what they’re seeing and what they need. And we support that as best we can,” said Mahoney. “The other piece is we’re staying very close to, and continuing to invest in emerging technology, connected cars, a big investment for us, electric vehicles and long term autonomous as well.”